Autostrade e ferrovie. Spazi di lavoro più sicuri e tempistiche contratte per una migliore produttività. Le centine automatizzate Maccaferri stanno portando ai fronti di scavo una nuova frontiera operativa
di FABRIZIO APOSTOLO
Il 30 novembre scorso, terzo giorno dell’evento celebrante i 50 anni dell’ITA e della SIG, con annessi ITA Awards 2024, i riflettori si sono spostati dal Palazzo Ducale di Genova, sede della parte convegnistica, ai cantieri di un’opera – il Terzo Valico dei Giovi – tra le grandi infrastrutture della rete TEN-T in corso d’i esecuzione. L’obiettivo: illuminare, in particolare, alcune tecnologie messe a punto e impiegate con il preciso scopo di migliorare gli standard di sicurezza (e non solo) nei contesti di lavoro in galleria.
In collaborazione con gli organizzatori e contando sull’ospitalità e sull’accoglienza del padrone di casa RFI (Gruppo FS Italiane), dell’appaltatore principale Cociv (Webuild) e dei progettisti (Cociv/Rocksoil), gli esperti di gallerie provenienti da tutto il pianeta hanno potuto osservare da vicino – a debita distanza di sicurezza – un concetto di centina automatizzata Made in Italy che ha salde radici (oltre un decennio di sviluppo e applicazioni) e un futuro contraddistinto da ulteriore evoluzione e crescendo di interesse, per esempio proprio sulla scena internazionale. La firma tecnologica: quella di Maccaferri, gruppo italiano e al tempo stesso globale diretto dal CEO Stefano Susani, e della sua Business Unit Tunnelling guidata da Nicola Faccioli.
La grande opera del Terzo Valico dei Giovi, per questa tipologia di centina, è dunque da considerare un vero e proprio laboratorio applicativo continuo di ingegneria civile ferroviaria, così come la rete di Autostrade per l’Italia lo è stato e lo è tuttora in ambito stradale. L’iniziativa pro railway, che ha avuto origine nel 2020 per prendere consistenza e ritmo dal 2021, rappresenta una risposta tecnologicamente avanzata a una domanda di sicurezza, efficienza produttiva e costanza di processo in un contesto in cui, per ragioni legate alla geologia, era stato necessario ricorrere a importanti interventi di puntellamento del fronte di scavo nell’esecuzione del rivestimento primario. Lo strumento per raggiungere questi obiettivi multipli: la centina automatizzata HEB 300 di Maccaferri, completa di dispositivo di giunzione automatico, di piede estensibile e catene automatiche.
Il 30 novembre, questa tipologia di centina è stata montata davanti al pubblico specializzato ITA-SIG in meno di 20 minuti inclusa l’installazione del puntone. Fattore tempo (da record) che, accompagnato al fattore spazio (di lavoro, completamente rinnovato) rende ragione di un nuovo, benefico paradigma: l’industrializzazione dello scavo tradizionale. .
Spazio sicuro e tempo produttivo
Iniziamo dallo spazio, ovvero dai rischi di sicurezza che la centina automatizzata va a minimizzare. Sia nel caso delle centine con e senza puntone, l’automazione dei meccanismi di collegamento dei componenti – inclusi quelli dei piedi, che nascono estensibili – fa sì che al fronte di scavo non vi siano lavoratori. Le centine vengono movimentate da mezzi d’opera, solitamente uno per il sostegno e uno per l’apertura della centina stessa. In generale, la centina può essere montata impiegando macchine già presenti in cantiere, il che rappresenta un vantaggio funzionale. Ma anche su questo fronte la ricerca sta lavorando su soluzioni ad hoc.
La scelta di utilizzare una centina automatica completa di puntone significa aumentare gli standard di accuratezza e precisione delle lavorazioni, nel rispetto della geometria progettuale. Inoltre, il loro utilizzo evita le rilavorazioni con benefici sia qualitativi sia proprio in termini di sicurezza.
Il tempo della posa è quindi estremamente velocizzato, come abbiamo visto, il che rappresenta una vera e propria leva capace di innescare il cambio di paradigma: “Rendere più rapida la posa della centina aumentando la sicurezza – spiega Nicola Faccioli, responsabile BU Tunnelling di Maccaferri – può costituire il primo passo per ripensare l’intero processo produttivo, in funzione di un miglioramento di tutti i suoi aspetti, qualitativi e quantitativi. La tecnologia, se inserita in una riorganizzazione delle attività al contorno, può generare davvero un circolo virtuoso capace di portare risultati importanti, per esempio in termini di aumento della produttività”.
Se negli ultimi decenni lo scavo meccanizzato ha segnato un punto di svolta in molti progetti di tunnelling, ora tocca al suo equivalente convenzionale toccare nuove frontiere, definire nuovi standard. Pienamente industriali. “E per farlo al meglio – aggiunge Faccioli –occorre essere consapevoli che è necessario un cambiamento culturale”.
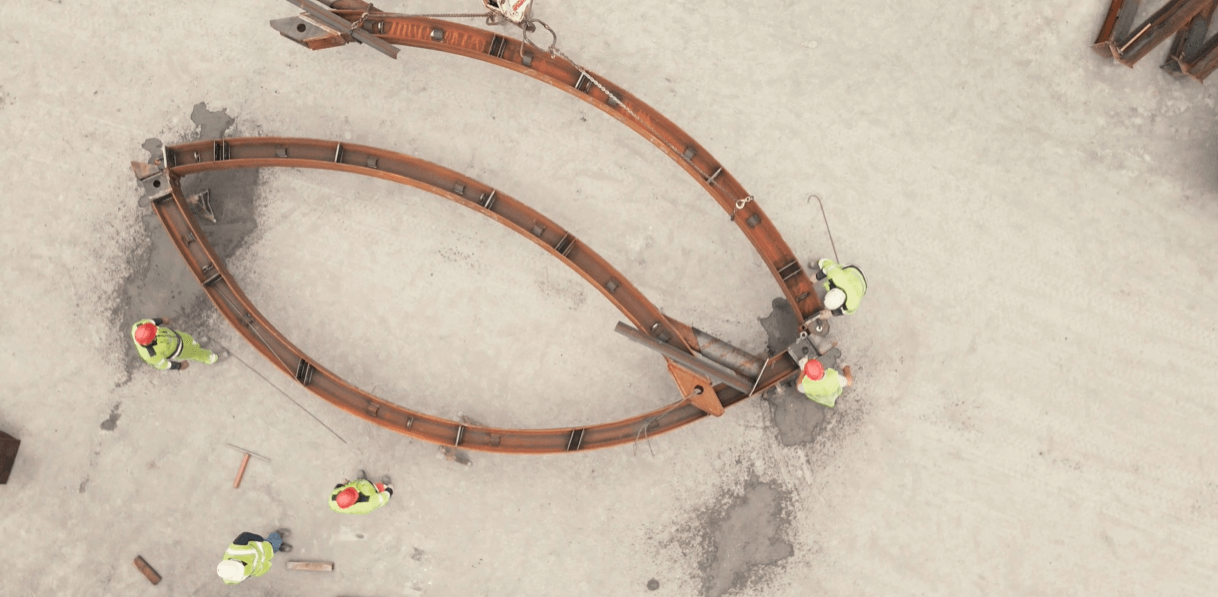
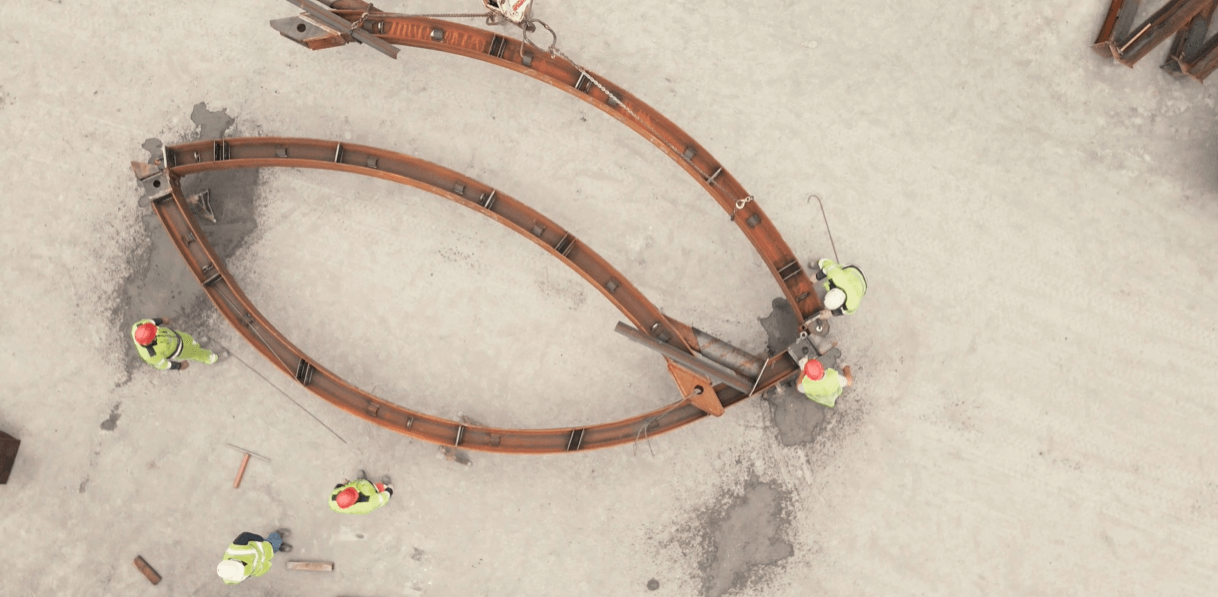
Innovazione al fronte
Dall’innovazione alla velocizzazione delle tempistiche, alla produttività complessiva aumentata. Dall’innovazione alla sicurezza. A proposito della prima, sempre con Faccioli e il team gallerie di Maccaferri possiamo aggiungere che le centine presto potranno diventare anche veicoli di conoscenza diretta, ovvero di approfondimento sia del contesto di scavo sia delle metodiche esecutive in atto: “I sensori collocabili sui nostri dispositivi tunnelling già oggi – conclude Faccioli – forniscono informazioni sulla correttezza dell’installazione. Maccaferri sta investendo molto su queste tecnologie IoT e la gamma di sensori offerta è molto ampia e spazia su diverse applicazioni in ambito geotecnico, con soluzioni avanzate di early warning systems e sistemi di monitoraggio”.
Le prime centine automatizzate Maccaferri sono state applicate nella loro versione tubolare sulla rete di Autostrade per l’Italia, correva l’anno 2012. Una best practice riconosciuta tra le altre: la galleria Boscaccio sull’A1, l’Autostrada del Sole, contigua alla galleria Santa Lucia, nota per il cospicuo impiego di tecniche di scavo meccanizzato (TBM). Qualche anno dopo, ecco la versione a profilo aperto, quella impiegata al Terzo Valico dei Giovi. Autostrade, dunque, e ferrovie: connubio a cui l’ingegneria del sotterraneo è solita dare vita. Oggi questa tecnologia continua il suo viaggio in autostrada, sulle strade statali e in altri siti ferroviari. In Italia e nel mondo. Maccaferri ha portato le sue centine sotto i riflettori del WTC 2024, in Cina. Quest’anno sarà la volta di Stoccolma, dove per il WTC 2025 di maggio sono in vista anche altre novità.
Tornando al Lontano Oriente, i suoi specialisti stanno attualmente lavorando ad alcuni progetti in Giappone, dove scenderà in campo una soluzione customizzata, ovvero in grado di accordarsi perfettamente ai meccanismi di avanzamento di scavo locali.
| ENGLISH EDITION
Industrializing conventional excavation
Motorways and railways. Safer workspaces and shortened time frames for greater productivity. Maccaferri’s automated tunnel rib, introduced over a decade ago and continually evolving, is bringing a new frontier to the excavation face.
On November 30 – the third day of the event celebrating the 50th anniversary of ITA and SIG – participants took a technical tour of the work sites for the Terzo Valico dei Giovi, one of the major TEN-T network infrastructure projects currently under construction. The goal was to highlight certain technologies developed and employed specifically to improve safety standards (and more) in tunnel work environment.
Thanks to the organizers, host company RFI (Gruppo FS Italiane), main contractor Cociv (Webuild), and the designers (Cociv/Rocksoil), tunnelling experts from around the world had the opportunity to see up close an automated tunnel rib concept Made in Italy, which already has a solid record (over a decade of development and field applications) and a future of continued evolution and growing international interest. The technology is by Maccaferri, an Italian yet global group led by CEO Stefano Susani, with its Tunnelling Business Unit headed by Nicola Faccioli.
For this type of tunnel rib, Terzo Valico dei Giovi is serving as a real continuous test bed for railway civil engineering – just as the Autostrade per l’Italia network has long done in the road sector. The railway-focused initiative, which began in 2020 and gained further traction in 2021, stands as a technologically advanced answer to demands for safety, production efficiency, and process consistency in a setting where, due to geological conditions, major front-of-tunnel support measures were required during installation of the primary lining. The tool making these multiple objectives possible is Maccaferri’s HEB 300 automated tunnel rib, equipped with an automatic joint device, extendable base, and automatic chains.
During the November 30 demonstration, this tunnel rib type was assembled in front of the specialized ITA-SIG audience in under 20 minutes, including installation of the invert strut. That exceptionally short timeframe, combined with the new and improved work area, underpins a beneficial new paradigm: the industrialization of conventional excavation.
Space (safety) and time (productivity)
Starting with ‘space’ – meaning the safety issues minimized by the automated tunnel rib – both systems, with and without invert strut, feature automated connection mechanisms for their components (including the feet, which are designed to extend), eliminating the need for personnel to stand directly at the excavation face. The ribs are maneuvered by site machinery – generally one machine to support them and another to open them. In most cases, the ribs can be assembled using equipment already on-site, which is a functional advantage; research is nonetheless ongoing into ad-hoc solutions.
Opting for a fully automated tunnel rib that includes a invert strut increases accuracy and precision in the work, maintaining alignment with the design geometry. Furthermore, the use of these technologies avoids rework, delivering both quality and safety benefits. Installation is therefore extremely fast, as we saw – acting as a lever that can drive a paradigm shift. “Making tunnel rib placement faster while also enhancing safety,” explains Nicola Faccioli, Head of Maccaferri’s Tunnelling Business Unit, “can be the first step in rethinking the entire production process to improve every aspect, both qualitative and quantitative. If this technology is integrated into a reorganization of the surrounding work steps, it can create a truly virtuous cycle, yielding significant results, for instance in boosting productivity.”
Over the past decades, mechanized excavation has brought about a sea change in many tunneling projects; now it is time for its conventional counterpart to push new boundaries, setting fresh, fully industrial standards.